
#Ansys apdl update
If you want to learn more about getting high quality images out of Ansys Mechanical at Ansys 2020R2 and newer, including 3D Printing your results, take a look at, An Update on Outputting Results from Ansys Mechanical.
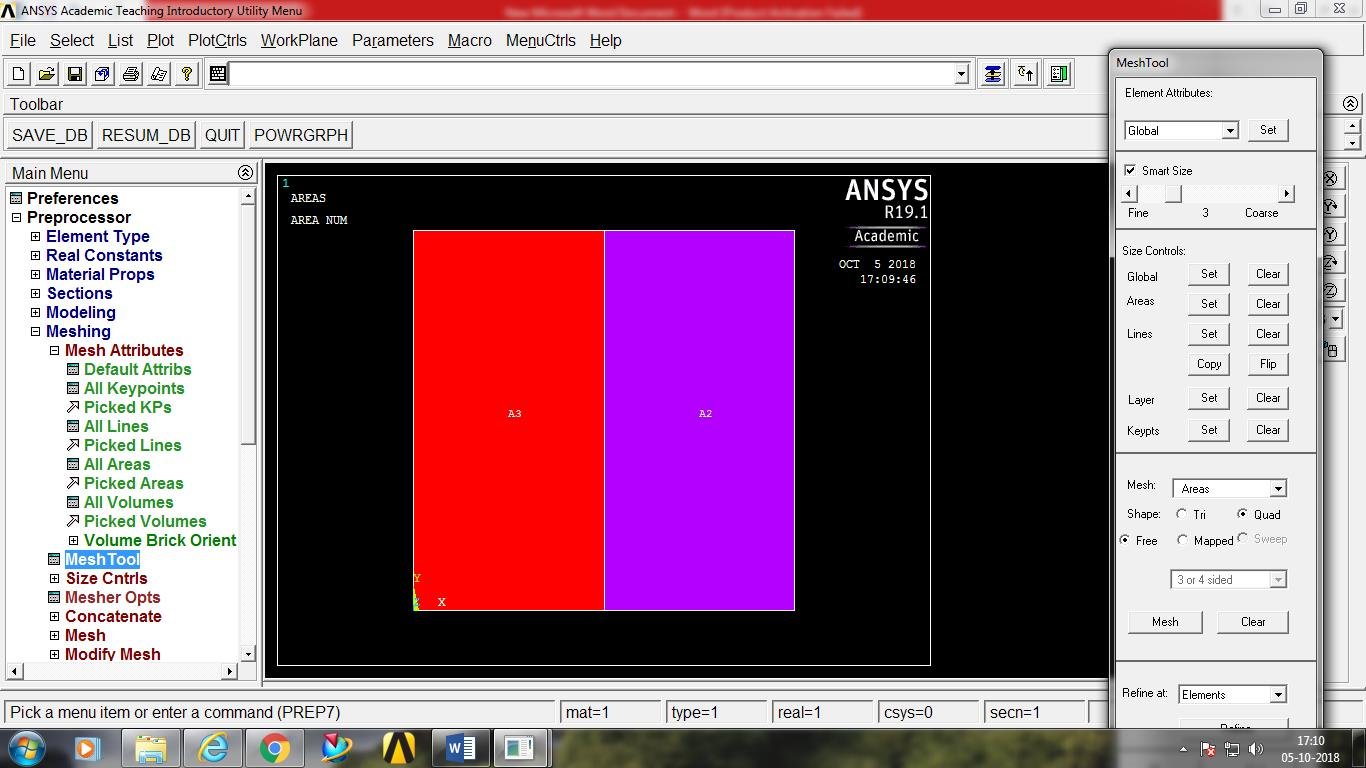
Switch to the solution processor by clicking Main Menu > Solution.It is intentionally large in order to force ANSYS to converge at each of the specified time steps. NEQIT, 1000 - This command specifies the number of equilibrium iterations that must be performed before ANSYS evaluates the need to reduce the time increment size.Multiple substeps help to identify when failure initiates and how it progresses as the load increases. plotting of MAPDL geometry and meshes using VTK from within a. Since the step time is 1, each substep time increment will be 0.02. scripting of MAPDL through both Python and Ansys Parametric Design Language (APDL) syntax. As ADPL and the ANSYS MAPDL environment (also known as ANSYS Classic) are based on different technology than ANSYS Mechanical products from Workbench/AIM. NSUBST, 50, 50, 50 - This command specifies the number of substeps to be used in the analysis.TIME, 1 - Specifies a step size equal to 1.PRED, OFF,, OFF - This command prevents ANSYS from using the converged solution at the last substep to estimate the solution for the current substep.NROPT, FULL,, OFF - This command instructs ANSYS to use the 'Full' Newton Raphson algorithm and prevents it from using the 'Adaptive Descent' algorithm.Enter the following commands into the command prompt:.You can elegantly expand the very extensive options by specifically adding APDL command objects (Ansys Parametric Design Language) to your Ansys Mechanical Setup. We have already created our model geometry and are now ready to modify the solution controls. Ansys Mechanical is a powerful tool with high ease of use, numerous functions and largely automatic selection of efficient and proven model settings.
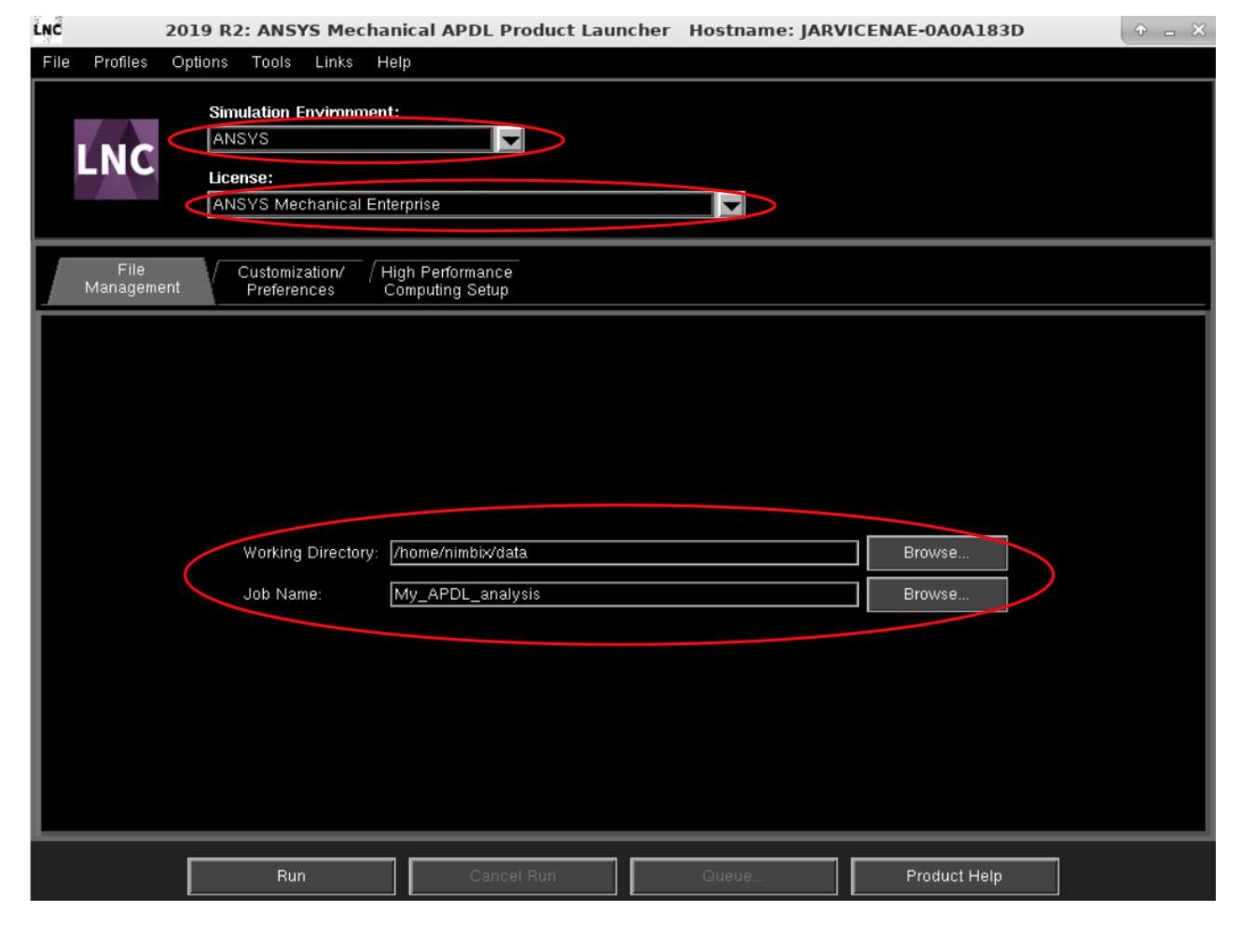
This results in a faster overall solution time. Specific solution control parameters allow for a solution with a decreased tendency for time increment cutbacks when used with Helius PFA. The default solution controls in ANSYS typically do not allow for an efficient solution in a progressive failure problem. Modify the parameters that govern the finite element solution to work optimally with Helius PFA.
